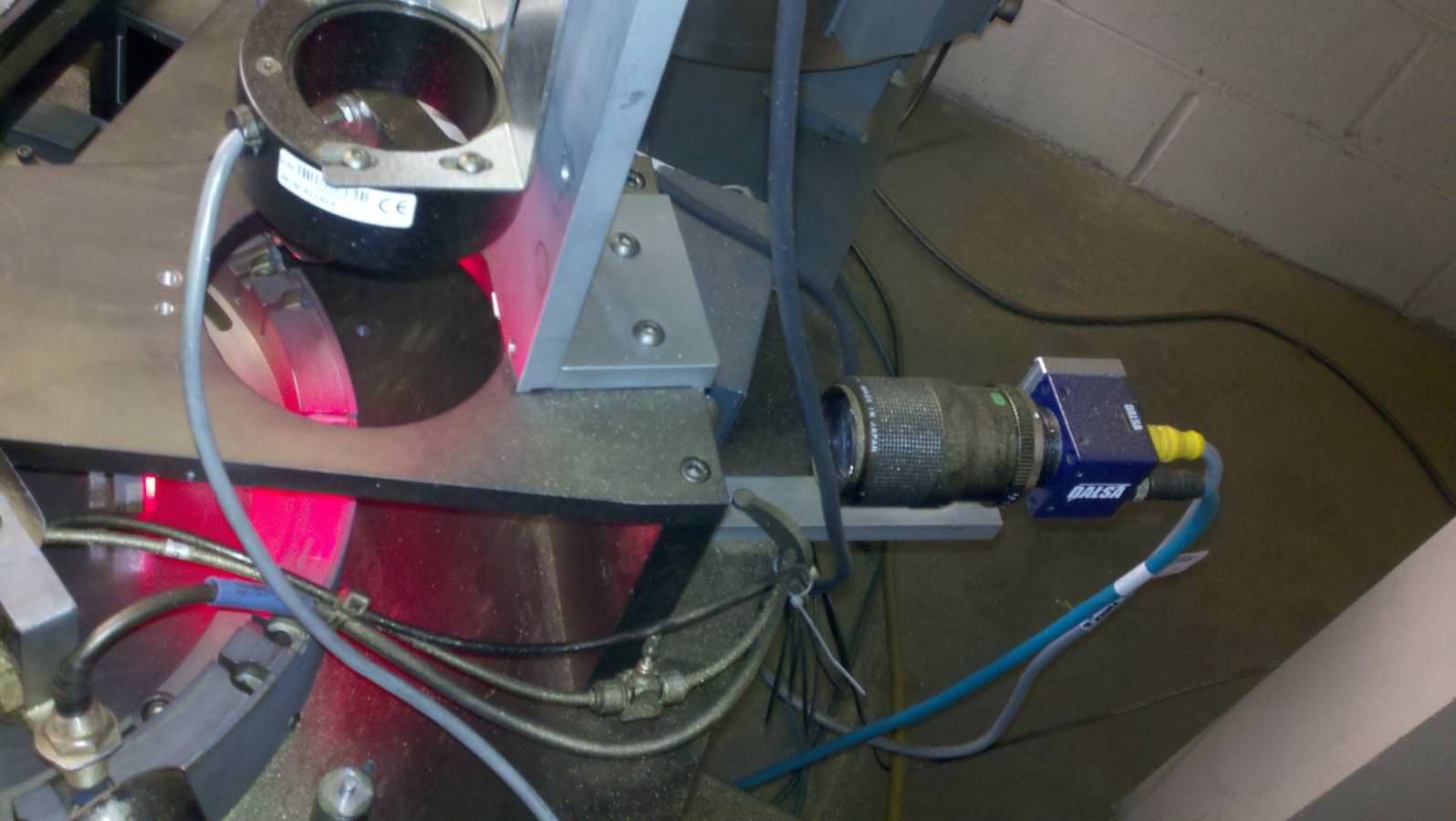
#Transports: Automotive/ Aerospace
Putting The Screws to a Challenging Vision Application
Established in 1967, Prime Engineered Components has two state-of-the-art facilities in Connecticut that manufacture precision turned products for industries ranging from aerospace to automotive
In its Watertown facility, Prime manufactures approximately 800,000 parts per week, primarily for automotive industry customers. Each part has to be flawless, or Prime runs the risk of costly and time-consuming returns, as well as strained relations with its customers. Using the compact, flexible, and economical BOA vision system from Teledyne DALSA, Prime has met its goal of 100% quality while making inspections easier for programmers and users alike to implement.
What industries would find this most relevant?
Automotive or transportation
Which of your engineering specialties does this project best illustrate?
Automated assembly
Vision systems (including image processing and OCR)
Describe the nature and scope of the project in greater detail
Searching for a Solution
“Our customers don’t require it but, since we know that our machines aren’t 100% capable and since our parts are produced too quickly for manual inspections, we elected to put vision in place for a multitude of dimensional inspections,” says Kathy Dibble, Director of Quality for Prime. “We would much rather remedy any quality problems in-house before product ships to our
customers.”
Prior to implementing the BOA solution, Prime had been using another manufacturer’s vision system in its Watertown plant to inspect components, the majority of which are knurled. These grooved and patterned parts present significant lighting and measurement challenges that Prime’s previous vision system wasn’t able to surmount.
Dave Turechek, the machine builder at Engineered Solutions who has worked on designing and integrating many of Prime’s machines, recommended a Teledyne DALSA solution.
Turechek worked together with Fernando Serra, Teledyne DALSA's vision specialist, to design a solution using Teledyne DALSA’s BOA vision system.
The BOA Measures Up
BOA is a highly integrated optical inspection tool for controlling quality and increasing productivity. It comprises all the elements of an industrial machine vision system - including sensor, light control processing engine, I/O, factory communications, developer and operator interfaces, and a protective IP67 enclosure- in a tiny (44 x 44 x 44 mm), smart camera-style package.
When designing the BOA solution, Serra incorporated new inspection criteria for gauging the outside dimensions of the knurled parts. Inspections of these parts are performed using the Caliper Tool in Teledyne DALSA’s iNspect application software. Embedded within the BOA, iNspect features an easy-to-use graphical interface and a toolset for a wide range of applications.
"This inspection couldn’t have been done without using the Caliper Tool,” says Serra. He first tried using a Rake Tool, but it was only able to provide an average of the high and low dimensions. “We needed to catch any of the really high points of the critical dimensions for greater precision,” says Serra. “The iNspect Caliper tool does this.”
In addition to its precision, the iNspect Caliper Tool is very user friendly. Prime’s Dibble, who does the verification runs and sets up the programs for the camera, says that the BOA’s ease of use and programming, along with its accuracy, were the primary reasons she decided to take a chance on a new camera.
Although more extensive data acquisition and networking are planned, this application currently is very straightforward: a proximity sensor triggers the BOA when a screw comes into the field of view. The camera takes an image of the screw and the Caliper Tool measures the outside dimensions of the knurled part to determine whether it passes or fails. Parts that pass continue on down the production line, while failed parts are removed manually from the rotary table where the inspection is performed, defects are verified, and the part is taken out of production.
“It’s a simple, streamlined machine vision application that has worked wonders for our quality control,” Dibble says.
Reaping Some Prime Benefits
The quality of the parts going out the door has increased dramatically since the BOA solution was implemented. Machine downtime stemming from frequent issues with the old vision system has been greatly reduced. In addition, Dibble and her team are thrilled with the ease of use of the BOA, in particular with the embedded iNspect Express interface. iNspect Express allows users to build solutions using a comprehensive toolset that is accessed via a web browser from a standard PC or laptop, and it connects directly to a variety of Ethernet-ready factory devices.
“We haven’t had a single glitch with the BOA system,” Dibble says.
Prime is installing two more Teledyne DALSA cameras for inspections on high-volume automotive inspection machines at its Watertown plant. “Teledyne DALSA’s technology has proven itself, and we feel confident that Prime and our customers will continue to benefit as a result,” Dibble concludes.