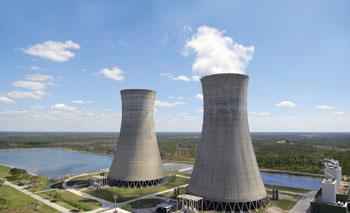
#Building and Construction
The Global Push for Zero
Now estimated to be worth $200 million, the Zero Liquid Discharge (ZLD) market is growing as stronger environmental regulations are being enforced. Countries such as China, India and Australia are employing technologies to maximise the full recovery of wastewater. Here the Orlando Utilities Commission shares experience from making an investment into the technology 30 years ago
While most industrial processes generate a wastewater stream, the objective of a Zero Liquid Discharge (ZLD) system is to recover and reuse all water, avoiding any liquid discharge.
The rise of ZLD can be traced back to the US in the 1970s. Specifically, as power plant discharge increased the salinity of the Colorado River, it created the regulatory context to push for ZLD in the US. At that time, new industrial projects seeking approval for discharge agreement could take several years; with ZLD, the timetable was cut to mere months. Since then, ZLD technology has taken hold and evolved significantly – in the US and around the world – over the last four decades.
The global goal of zero
Today, there are a rising number of evaporator/concentrator systems worldwide at work in a wide range of industries. Global construction of ZLD equipment represents an average of US$100-200 million of investment annually, according to industry analysts. ZLD technology has been mostly developed in Western countries for power plants, but continues to spread widely to drought stricken regions such as the Middle East and high pollution sensitive environments.
Generally, ZLD systems are employed where severe environmental constraints exist and/or where strong environmental regulations are enforced – either because an industry's activity is resource-intense, such as coal processing or petrochemical and mining, or because water resources are scarce. In coal rich, but dry North West China for example, ZLD is an ideal solution.
In India, water is a key priority with US$20 billion set aside for sewage treatment, irrigation and the recycling of water resources over the next five years. The establishment of a National Bureau of Water Use Efficiency (NBWUE) has been proposed with the objective of achieving a 20% increase in water use efficiency by March 2017. As part of this ambitious initiative, ZLD systems are mandatory for all inland thermal power units.
And in Australia, the world's largest coal seam gas-produced water treatment plant is a model example of maximising water resources while minimising environmental impact. The Kenya Central Water Treatment Plant (CWTP )is the most visible sign of Queensland Gas Company's US$1 billion investment in water infrastructure in the Surat coal basin of southern Queensland.
It is also one of two such plants that form part of QGC's Queensland Curtis LNG Project, the world's first project that has turned gas from coal seams into liquefied natural gas.
The process harnesses sophisticated computer-direct drills that pinpoint pockets of gas trapped in coal seams buried hundreds of feet underground. But because salt water mixed with the gas is sucked out to depressurise the seam, the drilling process risks contaminating groundwater used by farmers for agriculture – an industry integral to the local economy.
The Kenya CWTP comprises ultrafiltration, ion exchange, reverse osmosis (RO) and brine concentration technologies. Treating more than 90,000 m3/day, or the equivalent of that used by about 25 average-sized irrigated vegetable farms, the water treatment system treats coal seam gas produced water that is high in total dissolved solids, alkalinity and silica – water that generally would otherwise not be available for crops or drinking.
The plant, which includes an RO system of five trains designed for a recovery of 83-91%, is robust enough to meet stringent quality, recovery and reliability requirements, and flexible enough to allow for varying feed water quality.
As BG Australia Chairwoman Catherine Tanna commented, the Kenya CWTP will "help shore up supplies for town consumption and help landholders to grow crops that, in turn, support the government's aim to double food production by 2040".
Although often used to describe the technology and process, ZLD more accurately represents a goal: zero (or as close to zero as possible). There are multiple ways of achieving ZLD, with varying costs and complexity. As disposal of brine concentrate from water and wastewater treatment facilities becomes increasingly challenging and regulatory requirements continue to intensify, the awareness and adoption of ZLD and high-recovery technology is expected to increase. While the innovative solutions are just beginning to gain in popularity in many parts of the world, many facilities that showcase the power of ZLD have thrived for decades.
Empowering ZLD Technology: Orlando Utility Case Study
Even as Orlando, Florida grew from a small town into a vibrant city, the Orlando Utilities Commission (OUC) remained a strong, central community backbone, and has been for nearly a century. Still today, OUC's concern for the local ecosystem is as central to its business model as its ability to provide dependable, low-cost electric and water services to its more than 250,000 residential and commercial customers.
This is why, when first faced with water shortages and local, state and government mandates to conserve and protect drinking water in the mid-1980s, OUC decided to build a ZLD facility at its Stanton Energy Center.
Situated on thousands of acres, OUC's operations only occupy about one-third of the property; the rest is conservation land. The need to mitigate impact to wildlife is paramount. Likewise, the need to minimise water drawn from the Floridan Aquifer – one of the world's most productive aquifers in the world, which supplies water to several large cities, including Orlando – is a priority. These needs, as well as OUC's requirement to use municipal effluent from the local county as cooling tower makeup to help conserve water, all factored into OUC's initial – and subsequent – investment in ZLD.
"It's much more than wastewater guidelines," comments Jack Lyons, OUC project engineer. "We are always pursuing tighter site water balances and controls over each of the water streams onsite."
Based on the ability to meet reliability requirements and demand for more than 95% on-stream availability, OUC opted to employ a combination evaporation and crystallisation system. Onsite at the Stanton Energy Center, the cooling towers for four power generation units – two coal and two combined cycle units – blow down to a common retention pond (lined to prevent effluent discharge into the environment), which is used as the influence stream to the ZLD.
OUC's ZLD system uses four brine concentrator evaporators and four crystallisers to treat the cooling tower blowdown. The evaporative technology used here is a vertical tube, falling film evaporator driven by a mechanical vapor compressor. The evaporator technology enables a large volume of wastewater (95-98%) to be reclaimed as high purity distilled water, which is then usable in many industrial processes, such as for cooling tower makeup.
To achieve ZLD, forced-circulation crystallisers are driven by steam and used to reduce evaporator waste brine to dry solids, which is then locally landfilled.
Using wastewater from Orange County's Eastern Wastewater Treatment Facility as bulk scale cooling tower makeup, the evaporator and crystalliser technology takes the cooling tower blowdown stream that might otherwise end up being treated and discharged to the local surface water, and reclaims it for use as a clean water supply for makeup water to the cooling towers.
Importantly, OUC's ZLD design also builds in cross-connectibility, giving the municipal power company the benefit of flexibility. "Day to day, week to week, or month to month, we can move our process stream around from one process to another all within the ZLD plant to allow us to maintain a higher availability, keep the unit operating while we are doing maintenance and managing outages, " says Lyons.
With three different-sized process trains, the ZLD system can be scaled up or down depending on load needs (ability to choose which units are generating when) and local conditions (pond water levels).
The ZLD facility – which has been operational for more than two decades and includes three generations of ZLD technology – treats approximately 7.7 m3/ minute of cooling tower blowdown, converting the blowdown stream into high purity reuse water.
The ZLD component prevents the discharge of this wastewater stream, and maximises the reuse of wastewater to the greatest extent possible, which in turn limits the need for additional groundwater removal.
OUC is a modest organisation in terms of size and scale of its operations. Yet, it continues to thrive as one of the cleanest and most reliable coal-burning plants in the country. The cost of delivering power and water services is a complex equation, and OUC is below the median in the state. OUC generates electricity for more than 250,000 customers, producing over 1,800 megawatts of electricity.
"All of that production hinges upon the reliable operation of our ZLD plant," explained Lyons. "If we can't run the ZLD plant, we can't produce electricity."
Investing in ZLD
As with any advanced solution, ZLD carries concerns and key considerations. More than ever, however, the rewards seem to outweigh the potential risks. For one, ZLD is energy intensive; at the same time, it is very energy efficient. Likewise, the capital cost for ZLD is significant, and for some industries and municipalities, can be prohibitive. Yet, as Jack Lyons at OUC puts it: "Pay now or pay later...You have all types of options out there for water treatment," said Lyons. "But if you have a need for a high throughput, or extended operations, or high reliability, or great operational flexibility, or confidence in your process, look at ZLD. No one is going to put in a ZLD system and operate it for a year and shut it down…the benefits justify the cost in the long haul."
Advances in technology will continue to evolve and emerge, making ZLD and near-ZLD more affordable and more widely used in industrial and municipal applications, especially as regulations tighten on brine disposal. Global water scarcity is real. The need to optimise resources – water and energy – has never been more critical. ZLD's part in helping address this need will only continue to grow.
Lanny Weimer is global product manager - water and process technologies for GE Power & Water, and has more than four decades of direct engineering, project management, operations and marketing experience with complex water treatment and industrial wastewater treatment technologies.


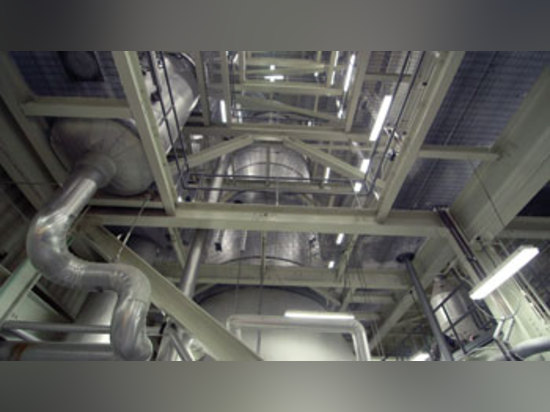